New Technique Boosts Efficiency, Sustainability of Large-Scale Perovskite Solar Cells
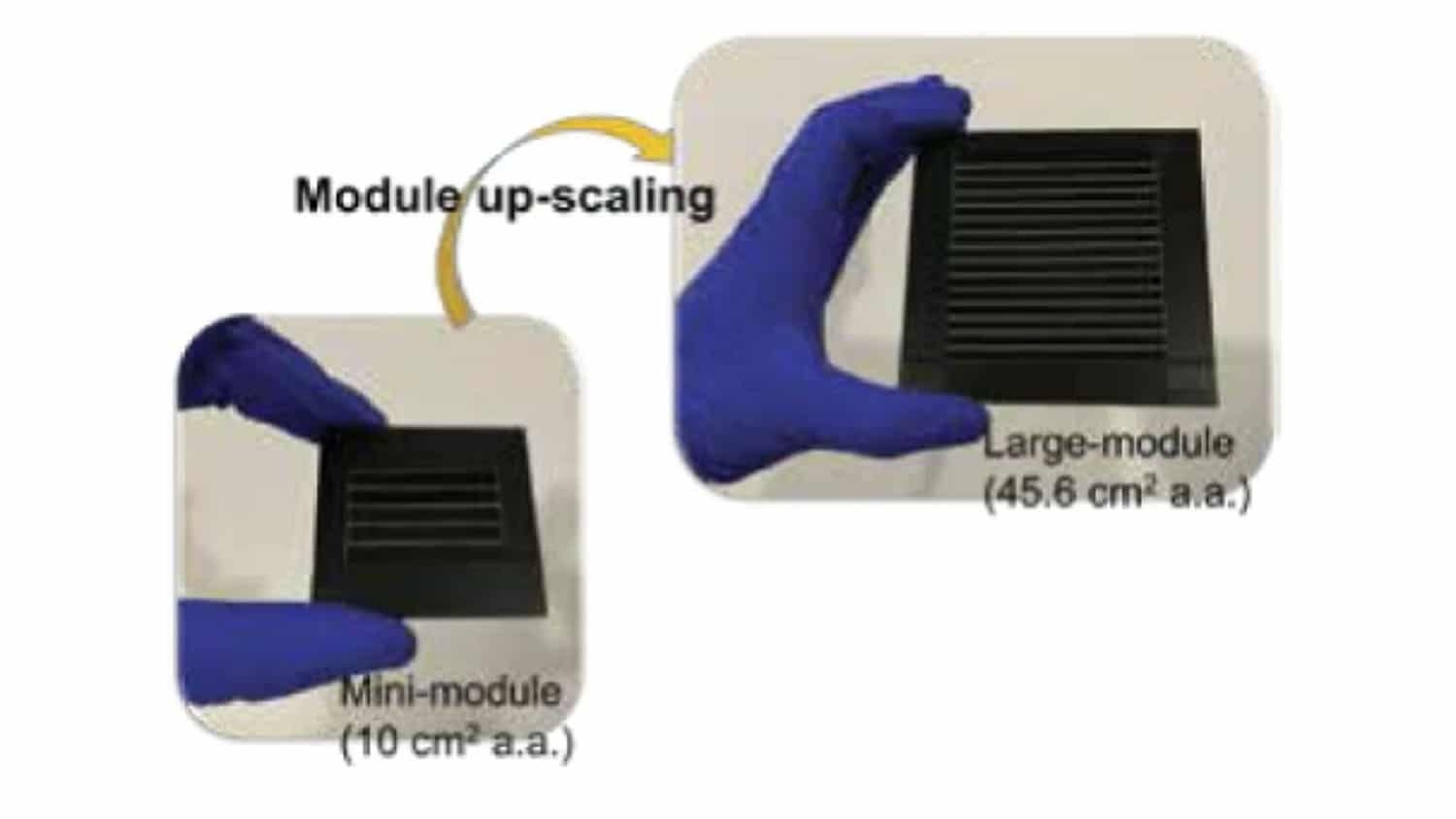
An international team of researchers has demonstrated a technique for producing perovskite photovoltaic materials on an industrial scale, which will reduce the cost and improve the performance of mass-produced perovskite solar cells.
The technique is low-cost, simple, energy-efficient, and should pave the way for creating perovskite solar cells. Perovskite is of interest for solar cells because it absorbs light very efficiently. This allows for the creation of lightweight, flexible solar cells that can be incorporated into a range of technologies, such as the windows of buildings or vehicles.
“In the lab, researchers produce perovskite photovoltaic materials using a technique called spin coating, which creates a thin film of perovskite on a substrate – but only on a small scale,” says Aram Amassian, co-corresponding author of a paper on the work and a professor of materials science and engineering at North Carolina State University.
“We’re talking about sample substrates that are only one or two centimeters square. However, people didn’t think it was possible to scale spin-coating up for manufacturing, using substrates that are tens of centimeters square. Instead, people have opted for a variety of other methods. But these other methods produce perovskite photovoltaics that don’t perform as well as the thin films made using spin coating and required significant research and development.”
“What we’ve done here is demonstrate that you can produce perovskite photovoltaics on larger substrates using spin coating by designing a co-solvent dilution strategy,” says Michael Grätzel, co-corresponding author of the paper and a professor at École Polytechnique Fédérale de Lausanne. “In other words, you can scale up production of photovoltaics and preserve the excellent performance of almost any type of perovskite thin film produced using spin coating.”
Historically, people thought spin coating could not be used to produce perovskite photovoltaics on industrial-scale substrates in a material-efficient way because of the nature of both spin coating and perovskites.
Spin coating involves placing a liquid on the surface of a substrate and then spinning the substrate, so that the liquid material spreads across the surface. However, when perovskite is applied using this technique, the solvents that keep the perovskite in a liquid state don’t evaporate quickly enough. This causes much of the perovskite to fly off the edges, meaning a lot of the perovskite material is wasted. It also results in irregular thickness of the perovskite on the surface, as well as some areas of the perovskite taking longer than others to dry. All of which is problematic from a manufacturing standpoint.
“Our approach tackles this challenge by introducing a co-solvent that allows the liquid perovskite to spread evenly and dry very quickly and uniformly,” says Hong Zhang of École Polytechnique Fédérale de Lausanne, who is a co-lead author on the paper.
The new technique also significantly reduces waste and, by extension, reduces toxic byproducts associated with manufacturing perovskite photovoltaics.
“The beauty of this technique is that many industries already use spin coating technologies to produce all sorts of products,” says Aldo Di Carlo, co-corresponding author of the paper and a professor at the University of Rome Tor Vergata. “Our work demonstrates that these existing technologies could be used to create perovskite solar cells. This could really accelerate the production and deployment of perovskite solar panels and cells.”
Collaborators on the demonstration project are already using the new technique to produce modules that are tens of centimeters across with excellent uniformity and performance.
“My team is now focused on using process automation and artificial intelligence to build on this work and further improve efficiency, stability and sustainability of perovskite photovoltaics,” Amassian says. “We’re hoping to work with public and private sector interests on finding ways to implement this work and accelerate the development of perovskite solar cell technologies.”
The paper, “A Universal Co-Solvent Dilution Strategy Enables Facile and Cost-Effective Fabrication of Perovskite Photovoltaics,” is published open access in the journal Nature Communications. Co-lead authors of the paper are Zhang; Kasra Darabi, a Ph.D. student at NC State; and Narges Yaghoobi Nia of University of Rome Tor Vergata.
The work was done with support from the European Union’s Horizon 2020 research and innovation program, the Swiss National Science Foundation, the Italian Ministry of Economic Development, and the U.S. Office of Naval Research under grant number N00014-20-1-2573.
-shipman-
Note to Editors: The study abstract follows.
“A Universal Co-Solvent Dilution Strategy Enables Facile and Cost-Effective Fabrication of Perovskite Photovoltaics”
Authors: Hong Zhang, Michael Grätzel, Anurag Krishna, Paramvir Ahlawat, Masaud Hassan S Almalki, Tzu-Sen Su, Viacheslav Bolnykh, Dan Ren, Lingfeng Pan, Sandy Sanchez Alonso, Shaik M. Zakeeruddin and Ursula Rothlisberger, École Polytechnique Fédérale de Lausanne; Kasra Darabi, Aram Amassian and Boyu Guo, North Carolina State University; Narges Yaghoobi Nia, Aldo Di Carlo, Luigi Angelo Castriotta and Mahmoud Zendehdel, University of Rome Tor Vergata; Ruipeng Li, Brookhaven National Laboratory; and Anders Hagfeldt, École Polytechnique Fédérale de Lausanne and Uppsala University.
Published: Jan. 10, Nature Communications
DOI: 10.1038/s41467-021-27740-4
Abstract: Cost management and toxic waste generation are two key issues that must be addressed before the commercialization of perovskite optoelectronic devices. We report a groundbreaking strategy for eco-friendly and cost-effective fabrication of highly efficient perovskite solar cells. This strategy involves the usage of a high volatility co-solvent, which dilutes perovskite precursors to a lower concentration (< 0.5 M) while retaining similar film quality and device performance as a high concentration (>1.4 M) solution. More than 70% of toxic waste and material cost can be reduced. Mechanistic insights reveal ultra-rapid evaporation of the co-solvent together with beneficial alteration of the precursor colloidal chemistry upon dilution with co-solvent, which in-situ studies and theoretical simulations confirm. The co-solvent tuned precursor colloidal properties also contribute to the enhancement of the stability of precursor solution, which extend its processing window thus minimizing the waste. This strategy is universally successful across different perovskite compositions, and scales from small devices to large-scale modules using industrial spin-coating, potentially easing the lab-to-fab translation of perovskite technologies.